These days, it is easy to see how much the demand for processed food products never ceases to increase. This change is forcing companies who make them to modify their production methods in order to better meet the new quality requirements.
Companies prefer faster chilling at lower temperatures in order to prevent any growth of bacteria and micro-organisms in foods. In the meat industry, this is even more important: thetemperature of the ambient air recommendedmust be maintained between 2°C and 5°C in order to prevent bacteriological growth.1
As well as a low work temperature between 2°C and 5°C,one of the most stringent requirements in the meat industry is to control humidity in a cold environment. In fact, at that temperature, controlling humidity is critical since the relative rate of humidity in the ambient air continues to increase during chilling. When the ambient temperature reaches the dew point, water condenses on cold surfaces such as walls, ceilings, work surfaces, etc. Companies have to avoid any condensation that could affect the safety of the foods produced.
According to ASHRAE standards, the relative rate of humidity (HR) recommended to avoid bacterial growth is 70% in the air in a plant at temperatures between 2°C and 5°C. However, toput a stop to the most resistant bacteria, 60%HRis preferable.
Dehumidification by condensation (chilling the air)
Until quite recently, the way of controlling humidity in the air of plants was to chill the air down to condensation. The water vapour in the air condensed on the chilling coils because the temperature was lowered below the dew point. The air vapour thus condensed in droplets and was then drained away. However, for supply air to be at a temperature of 5°C, the dew point for maintaining 70% HRis below the freezing point, i.e. -2.2°C. Under such conditions, thecooling coils of an air treatment unit would freeze and defrost repetitively, leading to a loss of efficiency.
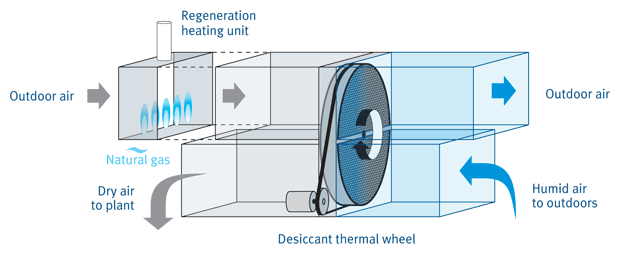
The usual method applied in a food plant is to ventilate massively with fresh air (100% fresh air) during the whole washing period. After the washing period, the plant has to start up again with temperature and humidity conditions close to those of the outdoors (30°C in summer and -20°C in winter).The air treatment units thus have to bring the air in the plant back to the required conditions (5°C and 70% HR) before production can start up again.
The chilling loads thus become very large, with the following consequences:
- Greater need for ventilation and motive force;
- Increased need for chilling;
- Higher electrical input power;
- Higher peak power demand;
- The time required for starting the plantup again varies, depending on outdoor conditions.
Desiccant dehumidification wheel
Air treatment units usingdesiccation do not need to condense water vapour. The moisture is adsorbed by a silica gel on the inside surface of a metal wheel that serves as substrate. The wheel is lined with perforated sheets through which the air passes (see Figure 1). How it works can be summarized as follows: air from the plant is recirculated through the wheel, which continues to rotate. The moisture in the air is adsorbed by the silica gel. The dried air is then chilled and returned to the plant.
The silica gel is regenerated by blowing a stream of warm air (120°C, or 250°F) across another a section of the wheel, turning the moisture adsorbed by the gel back into water vapour. The water vapour is thus expelled into the environment during the regeneration process. Usually, in industrialapplications, a direct fired heateris used to warm the regenerated air to 120°C.
Simulation
In order to compare the advantages of the two concepts, we simulated the design and operation of each method in a 40,000 ft² food plant (meat processing). Here are the results.2

Results and conclusion
Despite the fact that the two methods have advantages, it is much more cost-efficient to treat air and control humidity under difficult conditions when desiccation units are used. The results obtained are shown below.

Using a desiccant thermal wheel to dehumidify is particularly effective in an industrial setting since it can rapidly dry large quantities of water vapour. When ambient air conditions are severeand require the precise and efficient control of the rate of humidity, desiccant units on thermal wheelshave many advantages:
- Reduced need for ventilation
- Decentralized ventilation
- Air recirculation operational during washing periods
- Much lower demand for chilling
- Faster conditioning of air No defrost cycle
- Faster plant start-up
- Lower demand for motive force
- Lower power demand
- Lower electrical input power
While our analysis did not allow us to estimate construction costs, it is reasonable to expect a reduction in the case of a design using desiccation for the following reasons:
- Reduction in ventilation (motive force, ducts, etc.): 50%
- Reduction in chilling (system, piping, insulation, ammonia, etc.): 50%
- Reduction in electricity needs (input, compressor, motors, etc.): 56%
Finally, it is important to note that heat recovery on the desiccant units is eligible to apply to Gaz Métro’s energy savings program. Depending on the tariff policy in effect, i.e., 2012-2013, $85,000 in financial assistance3 would have been available for the four units needed for the simulation.
Roger Gauvin,Eng., CEM
Technical Advisor, DATECH Group
1 ASHRAE Handbook:Refrigeration (SI) 12.4 GrowthPrevention.
2 This comparative analysis was conducted in collaboration with Leprohon, a specialist in industrial refrigeration, and withDesertech, representing Munterdesiccating units.
3 Financial assistance granted in accordance with Gaz Métro’s Energy Efficiency Plan, as approved by the Régie de l’énergie. Some conditions apply. A Gaz Métro representative can tell you what assistance is available.
Continue reading