L’usine de Lantic est une raffinerie de sucre de canne. Elle produit du sucre blanc, de la
cassonade, du sucre liquide et du sucre de spécialité. Des travaux d’agrandissement terminés en
décembre 2000 ont porté la capacité de fonte de sucre de canne d’une moyenne de 35 tonnes
à 70 tonnes/heure.
Depuis ce temps, les gestionnaires veulent améliorer les performances énergétiques ainsi que la productivité. À ce jour, 512 000 GJ ont été économisés par rapport à 2005. La mobilisation des employés
et le soutien de Gaz Métro, jumelés aux programmes d’efficacité énergétique, ont aidé Lantic à atteindre ces résultats.
Agrandissement (décembre 2000)
Lantic exploitait une usine dans les Maritimes. La décision de transférer la production à l’usine de Montréal a été prise en 2000. Cette décision a eu des répercussions sur la capacité de raffinage, qui devait alors passer de 35 à 70 tonnes l’heure. Les préoccupations des gestionnaires ont donc porté sur l’atteinte de cet objectif. Après avoir consolidé leurs activités et acquis de l’expérience dans ce nouveau contexte, la vision des gestionnaires s’est tournée vers l’optimisation de la production et l’amélioration des performances énergétiques.
Premier projet majeur : la décoloration du sucre (été 2005)
Une des étapes du raffinage consiste à décolorer le sucre. La méthode utilisée traditionnellement dans les raffineries de sucre est de se servir du noir organique constitué d’os d’animaux calcinés. Le procédé consiste en une série de trempages et rinçages en cascade dans des vaisseaux dans lesquels se trouvent des lits de matières organiques carbonisées mélangées à de l’eau chauffée à 66 °C. Le sirop non décoloré est pompé et circule en série dans plusieurs vaisseaux afin de subir la décoloration spécifiée. Le sirop décoloré et dilué doit ensuite être concentré par évaporation en vue de l’étape suivante : la cristallisation.
Ce procédé de décoloration, très énergivore, requiert un grand volume d’eau chaude pour la dilution, et de la vapeur pour l’évaporation. Une importante mesure d’efficacité énergétique (MEÉ) a été implantée. Il s’agit de remplacer la décoloration utilisant du noir organique par un procédé par échanges ioniques.
Le procédé consiste à utiliser des vaisseaux remplis de matière synthétique, soit des résines de polymère. Le sirop est pompé et les résines agissent tel un aimant favorisant les échanges d’ions entre les minéraux et les résines. À la sortie des vaisseaux, le sirop est décoloré, et surtout, non dilué, déjà prêt pour la cristallisation. Une solution de saumure vient ensuite régénérer les résines épuisées, étape qui consiste à libérer et à rejeter les minéraux et à repolariser les résines. Ce premier projet avait une période de retour sur investissements (PRI) de 4 ans.
Intégration par analyse de pincement (été 2007)
Une importante étude a été réalisée afin de trouver tous les projets susceptibles de contribuer à améliorer l’efficacité énergétique de l’usine. L’optimisation et la production de la vapeur étaient ciblées. Le but était d’améliorer la compétitivité de l’usine et d’augmenter la productivité.
L’analyse de pincement requérait de mobiliser et de conscientiser le personnel à l’utilisation de l’énergie pour les procédés et les services. Les efforts ont permis de rallier les gens afin d’améliorer les performances. La collecte des données s’est avérée une importante mine d’informations et a permis d’initier la réflexion sur l’efficacité énergétique.
À la suite de l’analyse de pincement des procédés et des services, une série de projets rentables et intégrés d’économie d’énergie ont été identifiés. Un plan d’action a été précisé.
De l’analyse de pincement découlent des courbes composites permettant de déterminer le potentiel de récupération d’énergie en utilisant les courants des procédés puis ceux des services. Neuf projets ont été retenus pour des économies potentielles de l’ordre de 14 %.
Remplacement du brûleur de la chaudière no 4 (printemps 2009)
La chaudière no 4 produit environ 50 % des besoins de vapeur de la raffinerie. Il devenait alors primordial d’optimiser son efficacité. Quoique la chaudière soit dotée de plusieurs composants pour améliorer ses performances, tels un économiseur, un système de contrôle de combustion avancé, une sonde d’oxygène, un ventilateur d’air de combustion modulant, etc., le brûleur en place, d’une autre génération, devenait obsolète. Pour optimiser la conception d’un nouveau brûleur, des simulations de combustion en fonction de la dimension du foyer ont été effectuées pour maximiser la densité de chauffe, augmenter le transfert de chaleur et le rendement. Ce deuxième projet avait une PRI de 2,5 ans.
Récupération énergétique à la centrale thermique (printemps 2010)
Afin d’optimiser le fonctionnement de la centrale thermique, une analyse technique et financière a été effectuée. Elle a mis en valeur la nécessité de récupérer l’énergie contenue dans les produits de combustion. Le choix s’est porté sur un récupérateur à condensation hybride muni d’un brûleur au gaz naturel. Cet équipement permet de faciliter les activités de la centrale thermique en période estivale tout en garantissant une puissance nominale suffisante pour répondre efficacement aux demandes maximales de vapeur. La PRI était de 3,1 ans.
Optimisation des contrôles (2005 à 2011)
La centrale thermique et les différents procédés de l’usine sont dotés de plusieurs contrôles, et leur intégration a permis d’importants gains tant pour l’augmentation de la productivité que pour la réduction de l’intensité énergétique.
À la suite de l’analyse de pincement, un travail de stabilisation des chaudières et des procédés demandant de la vapeur a été entrepris, permettant ainsi de faire fonctionner la centrale thermique avec une chaudière en moins au début de 2007. Un gain de l’ordre de 4 % a été enregistré sur les consommations énergétiques.
Au début de 2008, le contrôleur électronique maître de la centrale thermique a été remplacé, ainsi que l’instrumentation. Cela a permis d’augmenter les possibilités d’amélioration, car plus d’informations étaient maintenant disponibles. On a révisé la variabilité des contrôles pour éviter les perturbations sur le réseau de vapeur. Ainsi, il y a moins d’écarts rapides quant à la demande de vapeur et les alarmes de bas niveau au ballon de vapeur ont aussi été réduites.
Au début de 2010, ces efforts, jumelés à l’installation du nouveau récupérateur, ont permis d’arrêter une deuxième chaudière et un dégazeur entre 6 et 9 mois annuellement, générant ainsi des économies annuelles additionnelles de 2 %.
L’arrêt de chaudière limite la disponibilité de production de vapeur et la marge de manœuvre. Toutefois, les efforts concertés des opérateurs de la centrale thermique et des procédés ainsi que du personnel lié à l’entretien assurent la fiabilité des opérations. La figure 1 illustre l’évolution de la performance énergétique.
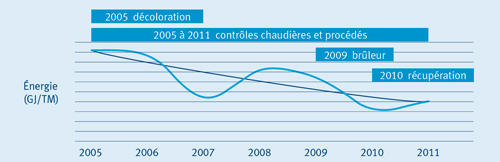
Conclusion
L’engagement du personnel ainsi que l’aide de spécialistes ont permis de maintenir la production de sucre raffiné à un niveau élevé générant des économies de 512 400 GJ depuis 2005.
D’autres projets retenus seront sous peu mis de l’avant dans une optique d’amélioration continue.
Guy Desrosiers, ing., CEM, CMVP
Groupe DATECH
Continuez votre lecture